Page History: Replacing the Arbor Bearings on the Delta Rockwell 12-14” Tablesaw (34-395)
Compare Page Revisions
Page Revision: 2008/04/02 16:38
by Mike Malone
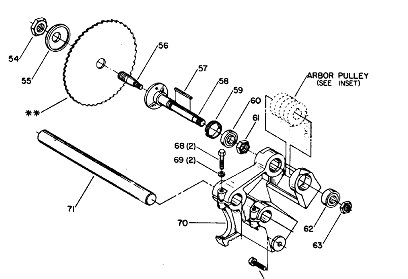
Disassembly
- Remove saw from powersource.
- This entire operation is best done with the tabletop removed from the machine. Remove the fence assembly and the 4 bolts holding the top onto the cabinet. I ran a chain around the top and gently hoisted it off with an engine hoist. (Make sure the top is secure during lifting as a fall will surely crack the cast iron!!) Place the top on a flat surface such as a garage floor.
- Put slack on the saw motor and remove the 4 v-belts.
- Remove blade nut and stiffener washer.
- Remove the end nut on the arbor #63 in drawing. Loosen the set screws holding the pulley to the arbor.
- Loosen completely, the collar #59 (use counterclockwise rotation). A Mallet and a square headed screwdriver work here, if the original $70. wrench is unavailable.
- Drive out the arbor by starting to tap the end of the arbor #58 with an appropriate tool (I used a 3/8" ratchet extension). Tap until the arbor is free of the housing on the right side. Bearing #62 will come off the arbor at this point.
- This should free the arbor from of the casting.
- As I said, the right side bearing #62, should come off easily.
- The Left side bearing #60, will have to be pressed off after removing the nut #61. And the 4-sheave pulley.
- Clean up the arbor as well as the bearing housings in the saw table casting.
- I was able to get the bearings locally. * NOTE: Delta are shipping as of 3/2002, NTN brand (Taiwan), #6204LB for the smaller bearing (dwng #62) and using INK brand (Japan), #3205J2Z for the larger arbor bearing. (dwng #60)
- You might consider, as I did, replacing #63 (nut $4.45) and #59 (collar $15.50) available from Delta.
Re-assembly
- Clean up the arbor after inspection. Thankfully, the arbor on the 12/14 saw doesn’t seem as susceptible to “fretting” (arbor wear), like that of the 10” Unisaw.
- Place Collar #59 on the arbor and have the new bearing #60 pressed onto the shaft. Note: Press this bearing on far enough to leave it covering 1 to 2 threads on the arbor. Tighten nut #61 up against the bearing. Do not over tighten!…just use firm pressure. Any slack will be taken up when collar #59 is tightened down, sandwiching the bearing between it and arbor nut #61.
- Insert the arbor (with the collar #59, pressed bearing #60 and bearing nut #61) through the cast housing from left to right, placing the pulley and pulley key on as you go. Right side bearing #62 is place into its casting seat and nut # 63 is hand tightened.
- At this point everything should be where it ought to be, with the pulley loose on it’s key. Nut #61 will be hidden from view in the bearing housing at this point.
- Tighten arbor collar # 59 using a clockwise rotation. Tighten it up against the bearing #60, but don’t fully tighten it yet.
- Tighten arbor end nut #63. This will assure that the bearing is snugly up against the stop on the arbor shaft. This nut should go on far enough to leave 1-2 threads showing on the outside end of the arbor. Snug arbor collar #59 down again and then make sure nut #63 is tight.
- A word about torque here, the nuts #59 and 63 should not be so tight as to crush the bearings. The Delta tech said “not overly tight”. I used the “oil filter technique”…that is, I snugged the nuts down and gave it another 1/2 turn.
- The arbor should spin freely and above all, quietly!!
- Align the arbor pulley to the motor pulley and tighten it. Install new motor belts and apply power. Listen for any noise…there shouldn’t be any!
- Replace the tabletop, align the top to the blade and reinstall fence.
The Tabletop
While I had the top off my machine, I took it to have it re-surfaced. I have heard of people sandblasting a top, but no one seems to recommend it. There are hard and soft particles in cast iron and sandblasting will effect the soft particles differently than the hard ones. The surfacing firm I used was Schaffer Grinding in Los Angeles (1-323-724-4476). After placing it on the Blanchard grinder it was discovered that the center was a little too high and too much metal would have to be removed during the grinding process.
I then brought it to Certified Steel Treating (1-323-583-8711). There, the center portion of the top was heated to 1500 degrees, a weight placed on the top and it was allowed to cool over several days. The top was then sent back to Schaffer for the final Blanchard grinding process. These grinders are large 9 foot diameter magnetic tables that rotate in one direction, while the grinder itself rotates in the opposite direction. You may be able to get your tabletop ground locally. But before you go hauling your top all over town, make sure you can find a machine shop or surfacer that can handle it. It all depends on the size of the tabletop and the size of the grinding machine. The surfacer must accommodate the largest dimension of the piece to be ground. This, of course, is the diagonal dimension of your tabletop. Best of luck on your projetc.