Description of the Steam Engine
      A steam engine is a motor which utilizes the energy of steam. It consists essentially of a piston and cylinder with valves to admit and exhaust steam, a governor for regulating the speed, some lubricating system for reducing friction, and stuffing boxes for preventing steam leakage.
      In its simplest form, the steam hammer, the steam acting on the piston lifts weights against the force of gravity.
      In the steam engine working as a motor continuous rotary motion of a shaft is essential. This is accomplished by the interposition of a mechanism consisting of a connecting rod and crank, which changes the to-and-fro or reciprocating motion of the piston into mechanical rotation at the shaft. A steam engine in which the reciprocating motion of the piston is changed into rotary motion at the crank is called a reciprocating steam engine to differentiate this form of motor from the steam turbine to be described later.
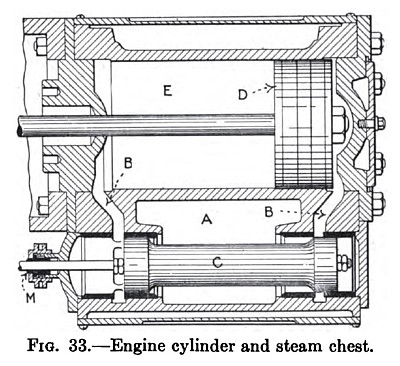 Engine Cylinder & Steam Chest |
| 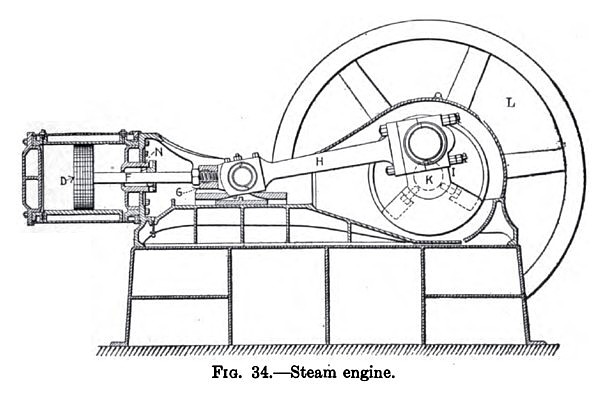 Horizontal Steam Engine |
|
      The various parts of a steam engine are illustrated in Figs. 33 and 34.
      Steam from the boiler at high pressure enters the steam chest
A, Fig. 33, and is admitted through the ports
BB alternately to either end of the cylinder by the valve
C. The same valve also releases and exhausts the steam used in pushing the piston
D.
E is the cylinder in which the steam is expanded.
      The motion of the piston
D, Fig. 34, is transmitted through the piston rod
F to the cross-head
G, and through the connecting rod
H to the crank
I, which is keyed to the shaft
K.
      The shaft is connected directly, or by means of intermediate connectors such as belts or chains, to the machines to be driven. The shaft carries the flywheel L, the function of which is to make the rate of rotation as uniform as possible and to carry the engine over dead-center. The dead-center occurs when the crank and connecting rod are in a straight line at either end of the stroke, at which time the steam acting on the piston will not turn the crank.
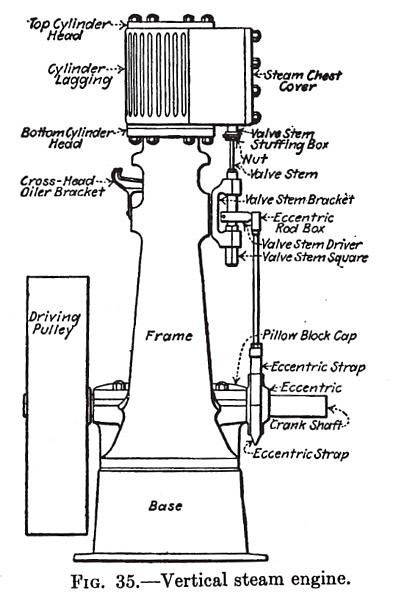 Vertical Steam Engine |
      A flywheel is sometimes used as a driving pulley, as shown in Fig. 35. The eccentric shown in Fig. 35 also rotates with the shaft. An eccentric is a crank of special form which imparts reciprocating motion to the valve through the eccentric rod and valve stem. The eccentricity of the eccentric is the distance between the center of the eccentric and the center of the shaft. The travel of the valve is equal to the throw of the eccentric, or twice the eccentricity. Changing the eccentricity changes the travel of the valve.
      Stuffing boxes which prevent the escape of steam around the rods are illustrated at
M and
N in Figs. 33 and 34.
      The size of a steam engine is given in terms of the cylinder diameter and length of stroke of the engine. Thus if an engine is called an 8-in. by 10-in. engine, this means that the diameter of its cylinder is 8 in. and its stroke or piston travel is 10 in.
Action of the Plain Slide Valve
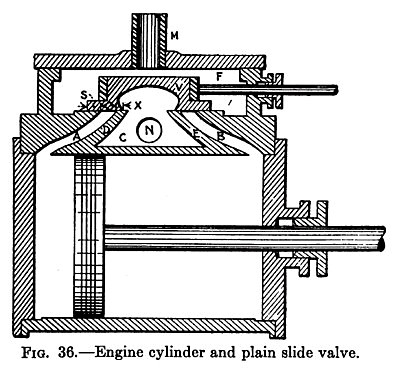 Engine Cylinder & Plain Slide Valve |
      The action of the plain slide valve will now be taken up in detail, as a thorough knowledge of this type of valve will enable one to understand all other forms. Referring to Fig. 36, which shows a section of a cylinder with the slide valve in mid-position,
A and
B are the steam ports, which lead to the two ends of the cylinder;
C is the exhaust space. The steam ports are separated from the exhaust space by the two bridges
D and
E.
F is the steam chest.
V is a plain slide valve, commonly called a
D slide valve. The amount
S that the valve
V overlaps the outside edge of the port, when in the middle of its stroke, is called the steam lap. Similarly the amount by which the valve overlaps the inside edge of the port when it is in mid-position is called the exhaust lap.
M and
N are the steam and exhaust pipes respectively.
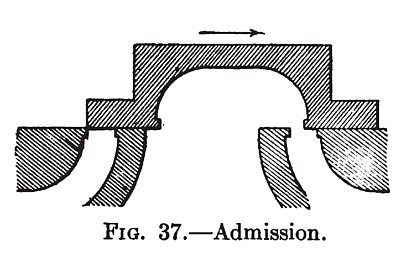 Admission |
| 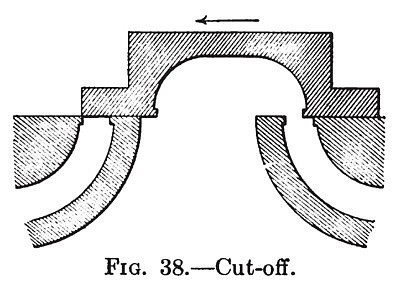 Cut-Off |
|
      The four valve events are: admission, cutoff, release and compression. Admission is that point at which the valve is beginning to uncover the port, as shown in Fig. 37. Cutoff occurs (Fig. 38) when the valve covers the port, preventing further admission of steam.
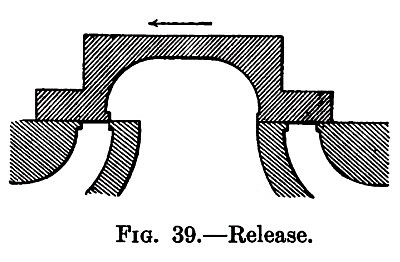 Release |
|  Compression |
|
      This is followed by the expansion of the steam until the cylinder is communicated with the exhaust opening, at which time release, as shown by Fig. 39, occurs. Compression occurs when communication between the cylinder and exhaust opening is interrupted (Fig. 40) and the steam remaining in the cylinder is slightly compressed by the piston. The valve is in the same position at cutoff as it is at admission, only it is traveling in the opposite direction. Similarly the positions of the valve are the same at release and compression.
      By lead is meant the amount that the port is uncovered when the engine is on either dead-center. The object of lead is to supply full pressure steam to the piston as soon as it passes the dead-center.
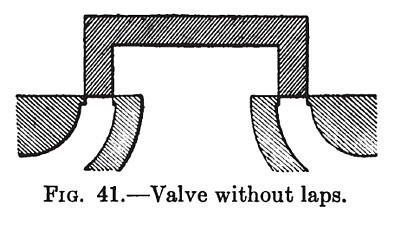 Valve Without Laps |
      If a valve is constructed without laps, as shown in Fig. 41, steam would be admitted to the cylinder at one end or the other and exhausted at the opposite end, if the valve is moved slightly in either direction. This would mean that steam admission at one end would take place throughout the entire stroke of the piston and would be exhausted from the opposite end at the same time. It is evident that a valve without laps will have no cutoff and steam will not be used expansively. To use steam without expansion is very uneconomical and is resorted to only in direct-acting steam pumps. For best economy a steam engine should be provided with a valve which cuts off at about one-third of the stroke.
Types of Steam-engine Valve Gears
      The simplest type of valve for steam engines is the single-slide valve, which controls the admission and exhaust of steam alternately to each end of the cylinder. The form shown in Fig. 33 is called a piston valve. In the position shown it admits steam to the head of the cylinder, the end farthest away from crank, and at the same time exhausts the steam from the crank end of the cylinder.
      Still a simpler type of valve, the plain slide valve, often used on portable and on traction engines, is shown in Fig. 36. The objection to this type of valve is that it is not balanced, and, either the friction of the valve on its seat is excessive, or the valve allows steam to leak into the exhaust space.
 Balanced Valve |
      This is remedied by the piston valve shown in Fig. 33, which is perfectly balanced, or by some form of balanced slide valves, illustrated in Fig. 42, which works between the valve seat and a balance plate with an accurate mechanical fit.
Valve Setting
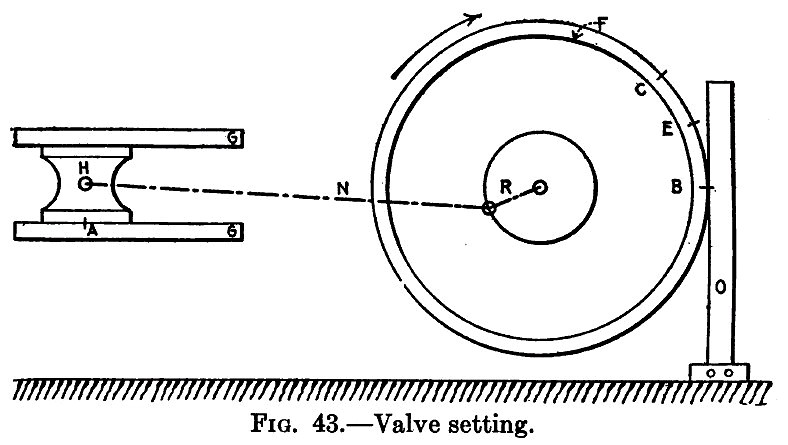 Valve Setting |
      The object of setting valves on an engine is to equalize as much as possible the work done on both ends of the piston. A valve may be set so that both ends have the same lead, or so that the point of cutoff is the same at both ends. Before a valve can be set, the dead-centers for both ends of the engine must be accurately determined. The method of setting an engine on dead-center can best be understood by referring to Fig. 43.
H represents the engine crosshead which moves between the guides marked
G,
N is the connecting rod,
R the crank,
F the engine flywheel, and
0 a stationary object.
      To set the engine on dead-center, turn the engine in the direction in which it is supposed to run, as shown by the arrow, until the cross-head is near the end of its head-end travel, and make a small scratch mark on the cross-head and guide, as at
A. At the same time mark the edge of the flywheel and the stationary object opposite each other, as at
B. Turn the engine past dead-center, in the same direction as shown by the arrow, until the mark on the cross-head and that on the guide again coincide at
A, and mark the flywheel in line with the same point on the stationary object, obtaining the mark
C. The distance between the two marks on the flywheel is now bisected at
E. If the mark
E on the flywheel is now placed in line with the mark on the stationary object, the engine will be on the head-end dead-center. Similarly the crank-end dead-center can be found.
      The stationary object may be a wooden board, or a tram may be used with one end resting on the engine bed-plate and with the other end used for locating the marks
B,
C, and
E on the flywheel.
      If a valve is to be set for equal lead on both ends, set the engine on the dead-center by the method given above, remove the steam-chest cover, and measure the lead at that end. Move the engine forward to the other dead-center and measure the lead again. If the lead on the two ends is not the same, correct half the error by changing the length of the valve stem, and the other half by moving the eccentric.
      To set an engine for equal cutoff, turn the engine until the valve cuts off at one end and mark the position of the cross-head on the guides. Then turn the engine until cutoff occurs on the opposite end and again mark this position of the cross-head on the guides. If the cutoff occurs earlier at one end than at the other, shorten the valve stem until the cutoff is equalized at both ends.
Steam-engine Indicator Cards
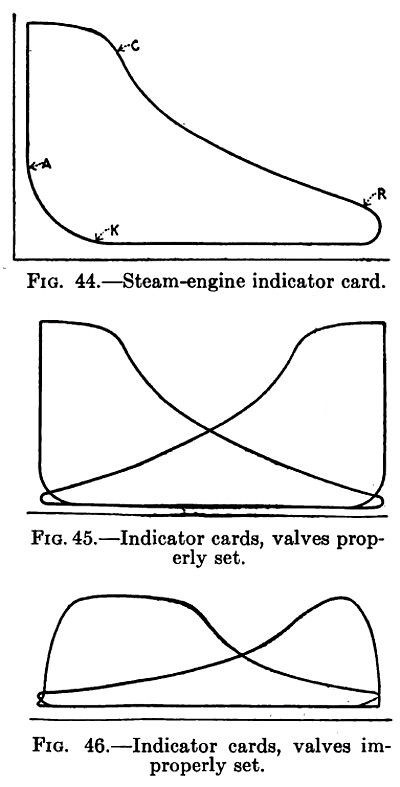 Steam Engine Indicator Cards |
      In general the best method of setting valves is by means of a steam-engine indicator. This form of instrument shows directly the action of the steam inside the engine cylinder, recording the actual pressure at each interval of the stroke. An indicator card taken by means of an indicator is shown in Fig. 44. The events of stroke on the card are marked: admission
A, cutoff
C, release
R, compression
K. Fig. 45 shows indicator cards taken from two ends of a cylinder with a valve properly set, while Fig. 46 shows indicator cards taken from an engine where the valve is poorly set.
Losses in Steam Engines
      The main losses in a steam engine are:
1. Loss in pressure as the steam is transferred from the steam boiler to the engine cylinder due to the throttling action in the steam pipe and ports.
2. Leakage past piston and valve.
3. Losses due to the condensation of steam in the cylinder during part of the stroke.
4. Radiation losses which take place when the steam passes through the steam pipes from the boiler to the cylinder and also while the steam is in the cylinder.
5. Losses of heat in the exhaust steam.
6. Mechanical losses due to the friction of the moving parts.
      Of the above losses those due to the heat carried away in the exhaust steam are greatest and are usually 75 percent or more of the heat supplied in the steam. Part of this heat can be used for such purposes as the heating of feed water before it enters the boiler, for heating buildings, or in employing the exhaust steam in connection with various manufacturing processes.
      The other great loss is that due to the condensation of steam, which takes place when the entering steam comes into contact with the cylinder walls, which are at the temperature of the exhaust steam. This loss can be reduced to a considerable extent by having the steam entering the cylinder as dry as possible. Another method for reducing this loss, which is used in connection with large engines, is to compound the engine.
      By compounding is meant the subdivision of the expansion of the steam into two or more cylinders. The steam on leaving the boiler enters the high-pressure cylinder, is partly expanded, and then enters one or more cylinders where its expansion is completed to the exhaust pressure. The range of pressures in each cylinder of a compound engine being less than is the case of a simple or one-cylinder engine, the temperature difference between the incoming and the outgoing steam is less. This lower temperature range decreases the condensation of the steam in the cylinder. The gain in economy does not usually compensate for the increased first cost of compound engines as compared with simple engines in small sizes.
      Radiation losses in the steam pipes leading from the boilers to the engines can be reduced to a minimum by covering the pipes. A good pipe covering will save the latent heat in the steam that would otherwise be lost, will keep the steam drier, and will pay for itself in a very short amount of time.
      The cylinders of most steam engines are now jacketed with some good non-conductor of heat and this loss is very small. Mechanical losses in steam engines can be reduced by proper lubrication. Oil can be applied to the various parts by separate sight-feed lubricators and grease cups. Another method is to connect an oil tank conveniently located with the various parts by adjustable sight-feed tubes, allowing different rates of feed to the various bearings. Still another method is to enclose some of the parts and make them self-oiling.
      The losses due to leakage past the piston and valves are usually very small in well-designed engines. The various forms of balanced slide valves can be kept tight by means of balance plates.
Steam-engine Governors
      The function of a governor is to control the speed of rotation of a motor irrespective of the power which it develops. In the steam engine, the governor maintains a uniform speed of rotation either by varying the initial pressure of the steam supplied, or by changing the point of cutoff and hence the portion of the stroke during which steam is admitted. Governors, which regulate the speed of an engine by varying the initial pressure of the steam supplied to the engine are called throttling governors. This is the simplest form of governor and is used mainly on engines of the plain slide-valve type.
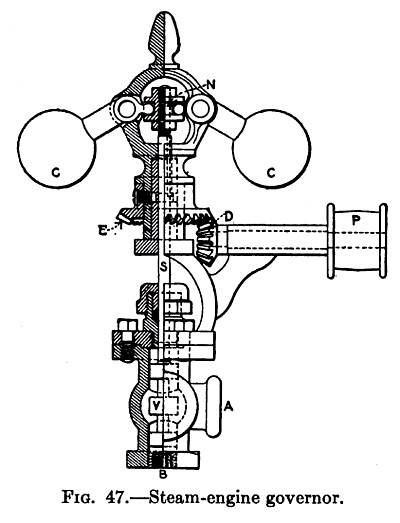 Steam Engine Governor |
      In Fig. 47 is given a section of a throttling governor, showing details. This form of governor is attached to the steam pipe at
A and is connected to the engine cylinder at
B, so that the steam must pass the valve
V before entering the engine. The valve
V is a balanced valve and is attached to a valve stem
S, at the upper end of which are two balls
CC. The valve stem and balls are driven from the engine shaft by a belt, which is connected to the pulley
P, and which in turn runs the bevel gears
D and
E. As the speed of the engine is increased the centrifugal force makes the balls fly out, and in doing so they force down the valve stem
S, thus reducing the area of the opening through the valve, and the steam to the engine is throttled. As soon as the engine begins to slow down, the balls drop, increasing the steam opening through the valve
V. The speed at which the steam is throttled can be changed within certain limits by regulating the position of the balls by means of the nut
N Most of the better engines are governed by varying the point of cutoff and hence the total volume of steam supplied to the cylinder. In high-speed automatic engines this is accomplished by some form of flywheel governor which is usually placed on the engine shaft, and which controls the point of cutoff by changing the position of the eccentric.
Engine Details
      The general construction of steam-engine cylinders can be seen from the previous illustrations. Steam
engine cylinders are made of cast iron. As the cylinder wears it has to be re-bored so as to maintain true inside surfaces. The thickness of the cylinder walls not only should be strong enough to withstand safely the maximum steam pressure, but should allow for re-boring. All steam-engine cylinders should be pro
vided with drip cocks at each end in order to drain the cylinder and steam chest when starting.
A good piston should be steam-tight and at the same time should not produce too much friction when sliding inside the engine cylinder. The piston is usually constructed somewhat smaller than the inside diameter of the engine cylinder, and is made tight by the use of split cast-iron packing rings. In Fig. 48 is illustrated a piston with its packing rings.
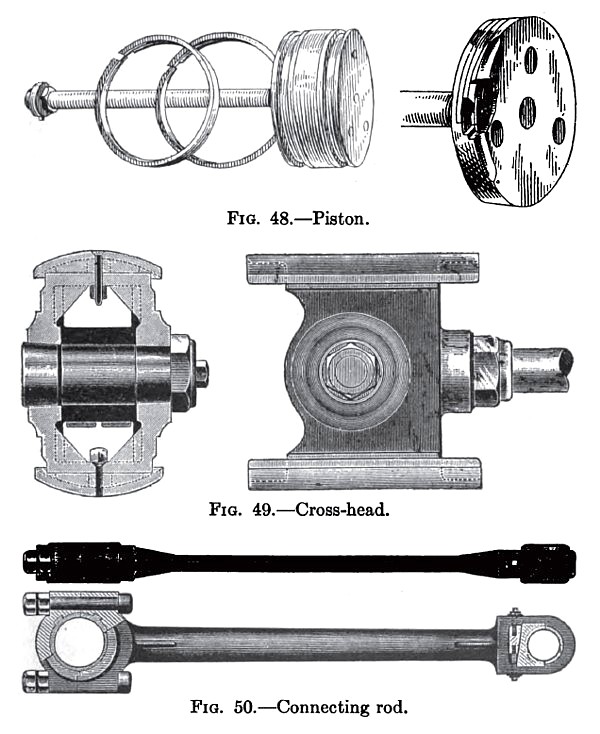 Piston, Cross-Head & Connecting Rod |
      The general construction of steam engine cross-heads is illustrated in Fig. 49. All cross-heads should be provided with shoes which can be adjusted for wear.
      Fig. 50 shows a connecting rod. It is connected at one end with the cross-head and at the other with the crankpin. A connecting rod should be so constructed that the wear on its bearings can be taken up. This is usually accomplished by wedges and set screws as illustrated.
      Some engines have their cranks located between the two bearings of an engine, and are called center-crank engines. Engines which have the cranks located at the end of the shaft and on one side of the two bearings are called side-crank engines.
      The eccentric is a special form of crank. It is usually set somewhat more than 90° ahead of the crank and gives motion to the valve or valves in the steam chest of the engine. The eccentric is a cast-iron disc through which the shaft passes and which gives motion to the valve.
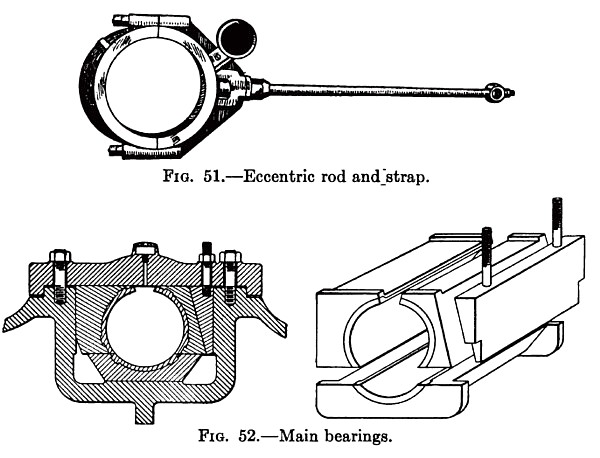 Eccentric Rod & Main Bearings |
      Fig. 51 shows an eccentric rod and strap. The main bearings of steam engines are illustrated in Fig. 52. These bearings are usually made in three or four parts and can be adjusted for wear by means of wedges and set screws fastened with lock-nuts.
Lubricators
      The subject of lubricating the moving parts of an engine was treated to some extent in connection with the discussion of mechanical losses in steam engines.
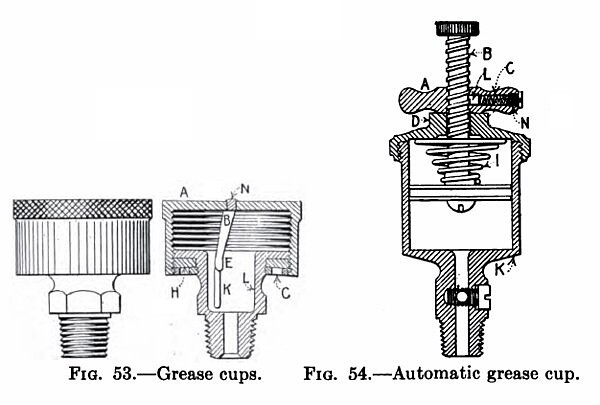 Grease Cups |
      Bearings may be lubricated by grease cups illustrated by Figs. 53 and 54. The first type is used on stationary bearings, the grease being forced out by screwing the cap down by hand. The type illustrated in Fig. 54 is automatically operated, and is used for the lubrication of crank-pins.
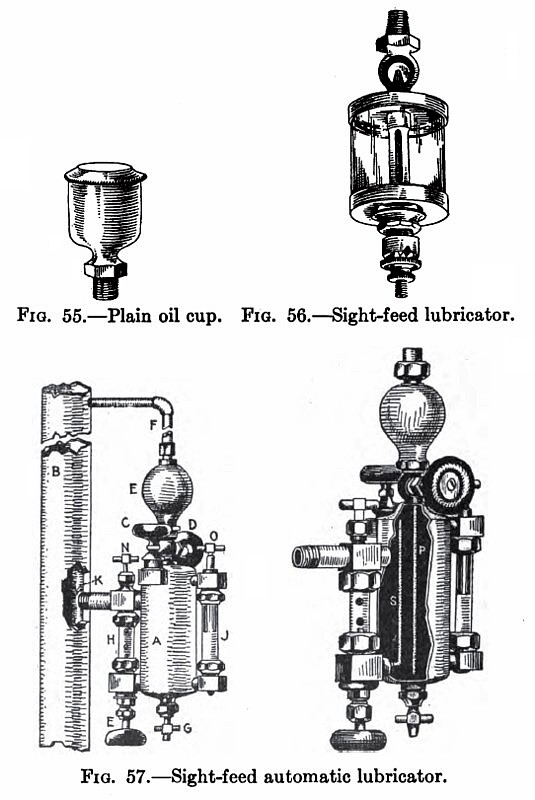 Oil Cup & Lubricators |
      If oil is used, a plain oil cup, illustrated in Fig. 55, can be employed, or some form of sight-feed lubricator, as shown in Fig. 56. By means of the sight-feed types the flow of oil can be regulated and the drops of oil issuing from the lubricator can be seen.
      For the lubrication of steam-engine cylinders some form of sight-feed automatic steam lubricator, as illustrated in Fig. 57, should be employed. This form of lubricator is used to introduce a heavy oil into the steam entering the cylinder. This oil is a specially refined heavy petroleum oil which will neither decompose, vaporize, or burn when exposed to the high temperature of steam. Steam from the pipe leading to the cylinder
B is admitted through the pipe
F to the condensing chamber
E, where it is condensed and falls through the pipe
P to the bottom of the chamber
A. The oil which is contained in chamber
A rises to the top, is forced through the tube
S, ascends in drops through the water in the gage glass
H, and into the steam pipe
K leading to the steam chest. The amount of oil fed is regulated by the needle valve
E.
T shows the amount of oil in the chamber
A.
      In order to fill the chamber
A, the valves on the pipes
F and
H are closed, the water is drained out through
G, and the cap
D is removed for receiving the oil.
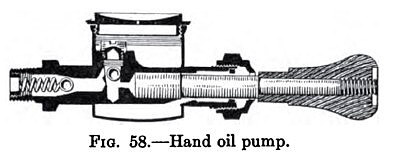 Hand Oil Pump |
      Fig. 58 shows a hand oil pump which is sometimes used to admit oil into the cylinder of an engine when starting.
Steam Separators
      The function of a steam separator is to remove any water which may be contained in the steam before it enters the engine cylinder. A separator placed in the exhaust pipe of an engine will remove a large part of the oil, making the exhaust steam more suitable for heating, manufacturing purposes, or for use in steam boilers after condensation.
      The importance of having the steam entering the engine cylinder as dry as possible was explained in an earlier part of this chapter. A good steam separator, if of sufficient size, will insure fairly dry steam and should be used in connection with all stationary steam engines.
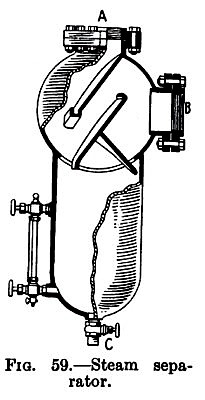 Steam Separator |
      Fig. 59 shows in section one form of steam separator. The wet steam enters at
A, strikes the deflecting plates, its velocity is decreased and the entrained water, which is heavier than the steam, falls to the bottom and is removed at
C by means of a trap. The dry steam passes out at
B.
The Steam Locomobile or Buckeymobile
      The locomobile, as built in Europe, and the Buckeymobile of the United States, is a self-contained power plant, which consists of a compound steam engine mounted upon an internally fired boiler. An insulated sheet-metal smoke box incloses both engine cylinders, a superheater, all steam piping and valves, and a reheater which imparts heat to the steam as it passes from the high- to the low pressure cylinder. This arrangement utilizes the heat in the flue gases for superheating the steam before it enters the engine cylinder, for reheating the steam between the high- and the lowpressure cylinder, for reducing heat losses within the engine and for cutting down the radiation losses of the entire power plant.
      The steam from the engine exhausts through a feed-water heater into a condenser, where it is condensed (converted into water) by direct contact with cold water or by contact with tubes through which cold water circulates.
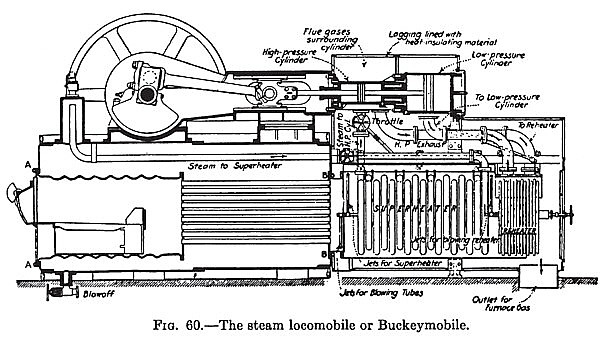 The Steam Locomobile or Buckeymobile |
      Fig. 60 shows a longitudinal section of a Buckeymobile with the various parts named.
This form of power plant has found a large field of application in Europe on account of its compactness and good fuel economy. The Buckeymobile, in small sizes, will no doubt in time be used to a considerable extent in rural communities in connection with flour mills, for irrigation pumping plants and for electric light plants in small towns. The principle of this type of power plant should also find successful application in connection with steam traction engines.
Steam Turbines
      The steam turbine differs from the steam engine described, in that it produces rotary motion directly and without any reciprocating parts. It consists of a stationary part and one or more wheels with vanes, which are rotated by steam striking the vanes. The elastic force of the steam, instead of acting on a piston, is exerted on the steam itself, producing a drop in pressure and a steam jet of high velocity.
      The steam turbine is best adapted for the driving of electrical generators, centrifugal pumps and air compressors, cream separators and other machinery requiring a high-speed rotation.
In large sizes the steam turbine is somewhat more economical than the reciprocating steam engine and occupies considerably less space. The steam turbine requires no internal lubrication, and thus the exhaust steam can be used again in the boiler without requiring oil filtration. For large power plants the steam turbine has several other advantages.
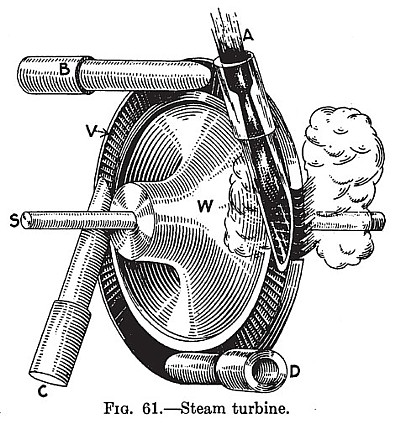 Steam Turbine |
      The action of one form of steam turbine used for the driving of cream separators is illustrated in Fig. 61.
A,
B,
C and
D are stationary nozzles in which the steam is completely expanded and strikes the vanes
V, giving a direct rotary motion to the wheel
W and also to the shaft
S.
Installation and Care of Steam Engines
      Foundations for stationary steam engines are usually put in by the purchaser, the manufacturer furnishing complete drawings for that purpose. Drawings of a board template are also included. A template is
a wooden frame which is used in locating the foundation bolts and for holding them in position while building the foundation. Before starting on the foundation a bed should be prepared for receiving it. The depth of bed depends on the soil. If the soil is rocky and firm, the foundation can be built without much difficulty. When the soil is very soft, piles may have to be driven. The ground for receiving the piles should be excavated to a depth of about 2 ft.
      The wooden template is then constructed from the drawings, holes being bored for the insertion of foundation bolts. Foundations may be built of masonry or of concrete. If of concrete the mixture should consist of 1 part of cement, 2 parts of sharp sand and 4 parts of crushed stone. The stone should be of
size as will pass through a 2-in. ring. In starting on a concrete foundation, a wooden frame of the exact shape of the foundation is built.
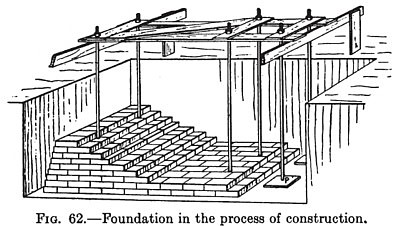 Foundation under Construction |
      This template is then placed in position in the manner shown by Fig. 62, and the bolts are put in, the heads of the bolts being at the bottom in recesses of cast-iron anchor plates marked
P. Often the foundation bolts are threaded at both ends and the anchor plates are held in place by square nuts. A piece of pipe should be placed around each bolt, so as to allow the bolts to be moved slightly to pass through the holes in the engine bedplate, in case an error should occur in the placing of the bolts, or in the location of the bolt holes in the engine bedplate.
      With the frame, template and foundation bolts in place, the concrete can now be poured and tamped down. After the concrete has set, the template is removed and the foundation is made perfectly level. It is well to allow a concrete foundation to set several weeks before placing the full weight of the engine on it.
When the foundation is ready, the engine is placed in position and leveled by means of wedges. The nuts on the bolts are now screwed down and the engine is grouted in place by means of neat cement, this serving to fill any crevices and to give the engine a perfect bearing on the foundation.
      After erecting the engine and all its auxiliaries, including pipes, valves, cocks and lubricators, all the parts should be carefully examined and cleaned, and a coating of oil should be applied to all rubbing surfaces, cylinder oil being used for the wearing parts in the valve chest and cylinder. Before the engine is operated for the first time, it is well to loosen the nuts and bolts, adjust bearings, and turn the engine over slowly until an opportunity has been given for any inequalities due to tool and file marks to be partially eliminated, and also to prevent heating that might occur if there was an error in adjustment.
      When the engine is ready to start, the boiler valve should be slowly opened to allow the piping to warm up, but leaving the drain cock in the steam pipe, above the steam chest, open to permit the escape of condensation. While the piping is being warmed up all the grease cups and lubricators are filled. Before opening the throttle valve, all cylinder and steam-chest drain cocks should be opened to expel water, and the flow of oil started through the various lubricators. The throttle valve is then opened gradually, and both ends of the engine warmed up. This can be accomplished in the case of a single-valve engine by turning the engine over slowly by hand to admit steam in turn to each end of the cylinder. In starting a Corliss engine the eccentric is unlocked from the pin on the wrist-plate and the wrist-plate is rocked by hand sufficiently to allow steam to pass through each set of valves. The drain cocks are closed soon after the throttle is wide open and the engine is gradually brought up to speed, provided steam is blowing through.
      When stopping an engine, close the throttle valve. As soon as the engine stops, close the lubricators, wipe clean the various parts, examine all bearings and leave the engine in perfect condition ready to start.
The above instructions apply to non-condensing engines. If the engine is to be operated condensing, the circulating and air pumps should be started while the engine is warming up. The other directions apply with slight modifications to all types of steam engines.
      In regard to daily operation, cleanliness is of great importance. No part of the engine should be allowed to become dirty and all parts must be kept free from rust. It is well to draw off all the oil from bearings quite frequently and to clean them with kerosene before refilling with fresh oil. In starting it is well to give the various parts plenty of oil, but the amount should be decreased as the engine warms up. An excess of oil should be avoided.
      Competent engine operators usually make a practice of going over and cleaning every bearing, nut, and bolt, immediately on shutting down. This practice not only keeps the engine in first class condition, as regards cleanliness, but enables the operator to detect the first indication of any defect that, if overlooked, might result seriously.
      If a knock develops in a steam engine, it should be located and remedied at once. Knocking is usually due to lost motion in bearings, worn journals or cross-head shoes, water in the cylinder, loose piston, or to poor valve setting. Locating knocks in steam engines is to a great extent a matter of experience and no definite rules can be laid down which will meet all cases.
      However, the beginner may, by careful attention to the machine, learn to trace out the location of a knock in a comparatively short time. He must, however, bear in mind that he cannot rely on his ear for locating it, as the sound produced by a knock is, in many cases, transmitted along the moving parts, and apparently comes from an entirely different point.
      A knock, due to water in the cylinder, is usually sharp and crackling in its nature, while that in the case of a crank or a cross-head pin is more in the nature of a thud. If the knock should be due to looseness of the main bearings, the location may be detected by carefully watching the flywheel, while if the cross-heads are loose in the guides the observer may be able to detect a motion crossways of the cross-head, but it is not likely that he can do this with accuracy in the case of a high-speed engine, and the cross-head should be tested when the engine is at rest.
     
In no case should any adjustment be made in bearings or moving parts of an engine unless the machine is at standstill or being turned by hand; never when under its own power
      The heating of a bearing is always due to one of five causes:
1. Insufficient lubrication due to insufficient quantity of oil, wrong kind of oil, or lack of proper means to distribute the oil about the bearings.
2. The presence of dirt in the bearings.
3. Bearings out of alignment.
4. Bearings improperly adjusted; they may be either too tight or too loose.
5. Operation in a place where the temperature is excessive.
      In case a bearing should run hot and it is very undesirable to shut down, it is oftentimes possible to keep going by a liberal application of cold water upon the entire heated surface or surfaces. It is sometimes possible to stop heating by changing from machine oil to cylinder oil, which has a higher flash point.
Should a bearing, particularly a large one, be overheated to the extent that it is necessary to shut down the engine, do not shut down suddenly or allow the bearing to stand any length of time without attention. This is particularly important in the case of babbitted bearings, as the softer metal of the bearings will tend to become brazed to, or fused with, the harder metal of the shaft, and it may be necessary to put the engine through the shop before it can be used again.
      In case of the necessity of shutting down for a hot bearing, first remove the load, then permit the engine to revolve slowly under its own steam until the bearing is sufficiently cool to permit the bare hand to rest on it.
      The presence of water in the cylinder is always a source of danger, and care should be taken that the water of condensation is thoroughly drained from the cylinder when the engine is first started, at shutting down, and at regular intervals throughout the operation. An accumulation of water may readily result in the blowing out of a cylinder head with its resultant loss to property and possibly of life. There are several appliances now on the market, which automatically safeguard the cylinder head by providing a weak point in the drain system, which will relieve the excess pressure before the cylinder head gives way.
Information Sources
- Farm Motors by Andrey A. Potter 1917 pages 42-64