Original article by "goosewing" (Gary McHugh)Introduction
Using the same tools and techniques as sweat soldering copper pipe, this is the best way I know of doing a permanent, almost invisible repair to sheet metal. By comparison, high temp soldering (brazing) is guaranteed to warp and buckle the metal. And with Mig welding, you risk blowing out more metal than you fill, plus the weld can be as hard as a rock.
As usual, careful and thorough preparation are key to good results, as well as meticulous attention to dressing the completed soldered patch to the surrounding metal. This technique isn't limited to filling errant holes drilled in sheet metal, by using some ingenuity, large hack jobs can be repaired, and a panel that otherwise would have to be replaced can be saved.
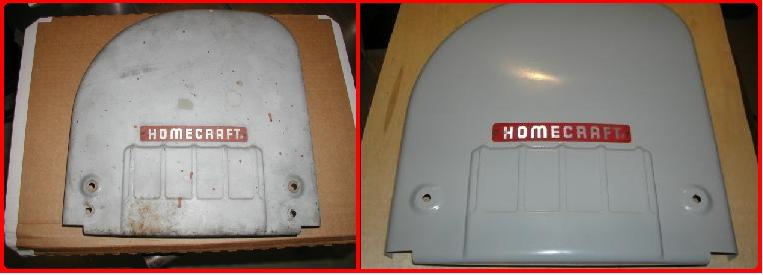 before and after |
You'll need everything that's typically used with sweat soldering copper pipe, a propane torch, plumbers solder, paste flux, small wire brush, plus some scrap copper or brass sheet metal. (copper pipe hanger fittings are good.) If you've never soldered before, (apparently southerners are about as familiar with copper pipe as they are with brown eggs.) a trip to the plumbing department is in order, and you'll find it's easy getting the hang of it after a few practice runs. Also handy: wire cutters, a hammer and dolly, double-cut mill file, sandpaper or emery cloth, Bondo.
Getting Started
The upper wheel guard of a small Homecraft band saw is the subject. The cover had two holes drilled into it by a previous owner, ( I figured out later this was to accommodate off-the-shelf blades from the big box stores. ) The screw knobs dug in and dented the metal, which didn't help any, and overall, it ranked highly as an un-esthetic modification. This is very thin sheet metal, 22 gauge, much thinner than let's say a Unisaw cabinet, so it's a good test subject. ↓
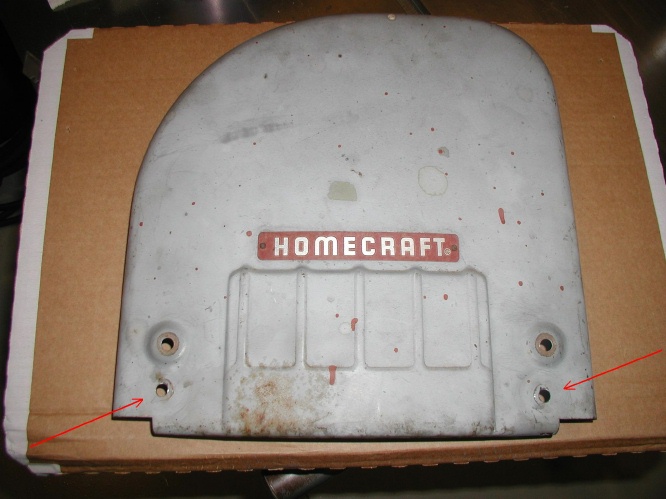
Prep
I first stripped the finish using TSP in hot water soak, then went to work tapping the burrs flat using a hammer and dolly, and cleaned around the area thoroughly with a wire brush.
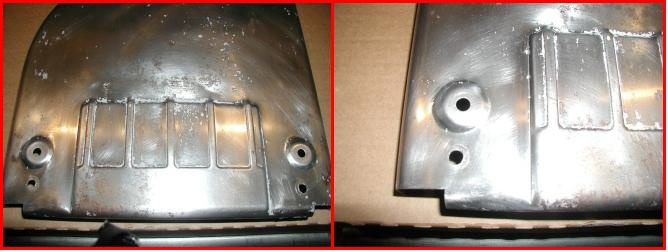
A filler for the holes is needed, I used some soft copper from a pipe hanging fixture, hammered flat it was a perfect thickness for this application. For thicker sheet metal, an old copper penny might be a quick source of material. Using lineman's pliers, the plug is cut to shape, slowly snipping into a circle. When I got to where it fit, I pressed it into the hole using the same pliers.
Soldering
I found you've got to back up the plug with something while you solder, or it will fall out at the worst possible moment. As a backer, I used my steel dolly.
With a propane torch, heat the area slowly, testing with the solder, (often times you can see the heated steel "flash" over when the time is right) Regardless, when the solder will stick, you're ready. Apply a dab of flux and while keeping the heat up, solder a nice bead over the area.
It takes about 5 - 10 seconds of heat to get the solder to flow, maybe longer for heavier gauge metal.
No need to apply solder to the other side. ↓
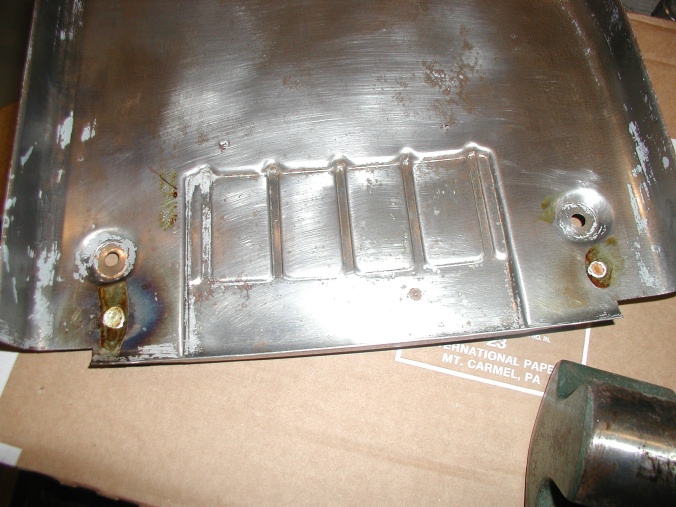
↑ While getting the solder to flow, you may want to lift the sheet metal a bit off your backer, which can act like a heat sink. That problem is evident on the left side of the above photo.
Filing and Sanding¶
The solder and copper are much softer than the steel, so dressing it goes fast and easy.
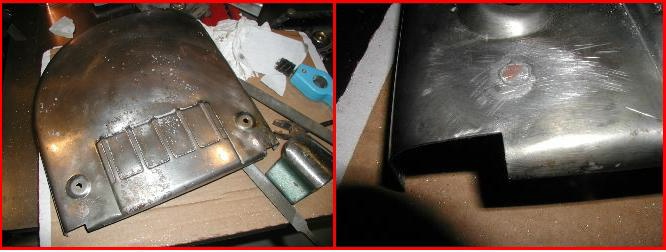
The rest is filing smooth, checking and rechecking with a straight edge. Any small divots are filled with bondo and sanded smooth.
The finished product
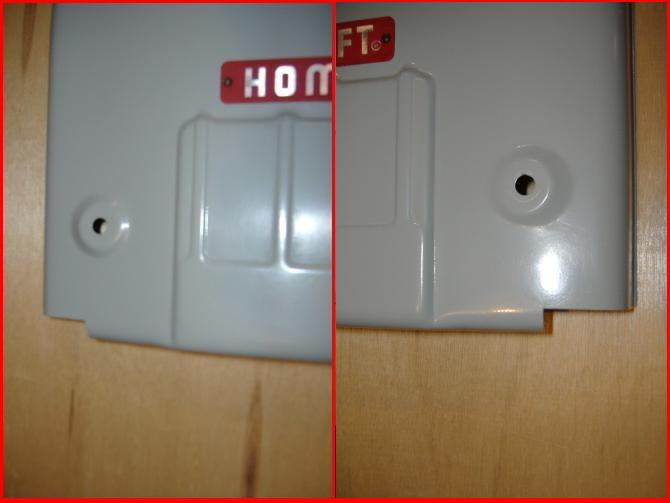
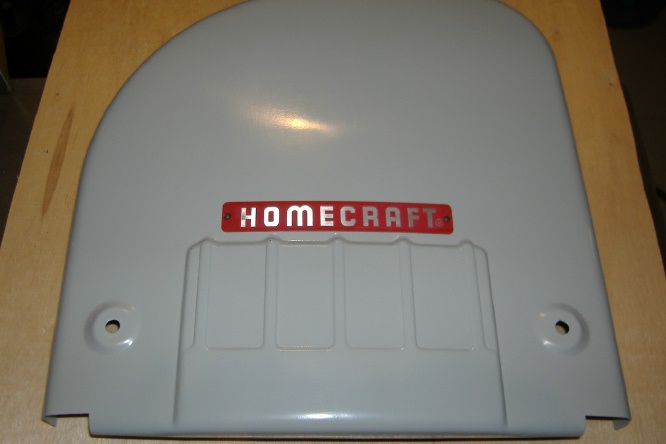
Repair invisible, both sides !
Remember:Do all metal hammering and straightening first.
Clean area well.
Take your time cutting the plug to fit, solder doesn't like to fill gaps too well.
Heat the sheet steel, not the solder.
Addendum:Just a couple quick notes on soldering. Heating time will vary quite a bit depending on material thickness. I was soldering some 11 gauge sheet steel (0.1250"), and it took about 2 minutes of heat before the solder would flow. That's about as thick as you'll probably find (1/8" thick !), by comparison a Unisaw cabinet is 14 gauge, about 0.08 inches thickness.
When filling thick sheet metal like that I let the copper plug stay a little proud on the show side and dressed it down, the back side I filled with polyester filler (Bondo.)
And, as it deserves repeating, I can not over-emphasize the importance of cleaning the sheet metal thoroughly before soldering. Every time I've found myself hurrying and doing a cursory job I end up with solder not sticking and rolling off, wasting both time and material and making myself feel foolish. Bring the area to a bright shine with sandpaper, wire brush, emery cloth, whatever floats your boat.